Research and development of high-performance next-generation ECM machine
Development of next-generation electrochemical machining (ECM) to realize high efficiency machining of difficult-to-machine materials with more complicated geometries and higher accuracy.- Research institute
- The University of Tokyo, Tokyo University of Agriculture and Technology, Shizuoka Institute of Science and Technology, HODEN SEIMITSU KAKO KENKYUSHO CO.,LTD., Kanto Gakuin University, Toyota Technological Institute, Makino Milling Machine Co., Ltd., ACRITECH CORPORATION
Background
Electrochemical machining (ECM) has advantages that it is possible to perform complicated shape processing and microfabrication with high efficiency, even for cemented carbide, titanium alloys, nickel base superalloys, etc., which are difficult to cut. In addition, high-speed machining of smooth surface without a heat affected zone or residual stress can be performed, which cannot be achieved by electrical discharge machining (EDM). For that reason, applications in the Europe and the US where the aircraft industry is popular are progressing.
On the other hand, bubbles and electrolytic products generated in the machining gap interfere with the electrolytic current, so it is difficult to obtain a uniform gap width, thereby high precision machining is difficult. Therefore, skill and trial and error are necessary for designing tool electrode geometry considering nonuniform distribution of the gap width and for jig design to obtain uniform flow field of electrolyte. For this reason, R&D concerning ECM has been stagnant in Japan, which has an industrial structure centered on manufacturing of dies and molds, automobile parts, and electrical and electronic equipment. Thus, standalone ECM machines have not been produced by machine tool builders.
Therefore, under this theme, we are working on research and development that surpasses the conventional ECM technology level, which is being advanced mainly in Europe and the United States.
Goals
Establishment of highly efficient and highly accurate ECM system(Figure 1).
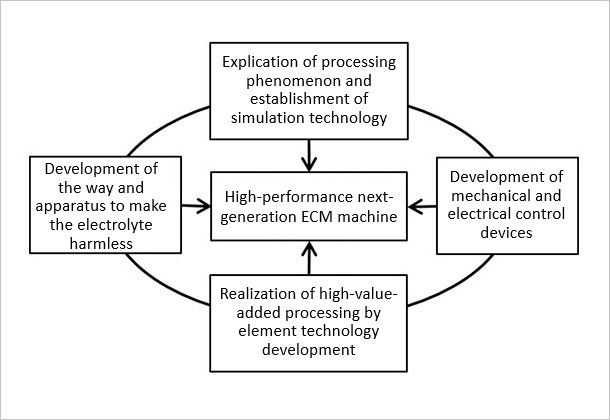
- Improvement in processing speed and processing precision in processing difficult-to-machine materials such as cemented carbide and nickel base superalloys.
- Improvement of processing speed by 40% or more and processing accuracy by 40% or more (relative to conventional). Achieve surface roughness of Ra 30 nm using the advantage of the atom by atom removal mechanism (Figure 2)

Implementation contents
- By direct observation of machining gap using transparent electrode, we clarify ECM phenomena and develop flexible and highly accurate ECM simulation tool which does not require trial and error(Figure 3).
- In order to solve the electrolytic solution treatment problem, we develop a compact processing apparatus that does not discharge hexavalent chromium.
- We develop elemental technologies such as electrolytic processing technology for difficult-to-machine materials and nonconductive materials such as cemented carbide, titanium alloy and nickel base superalloy, complex shape processing, curved hole processing, and micro electrochemical machining.
- Development of 5 axis ECM machine equipped with simulation tool, processing database, high performance pulse power supply, and environmentally friendly electrolytic solution treatment system.
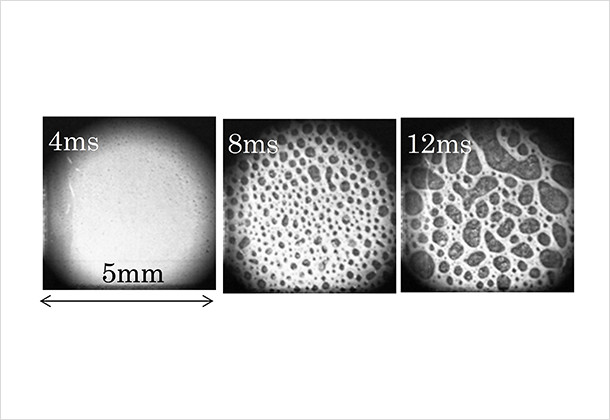